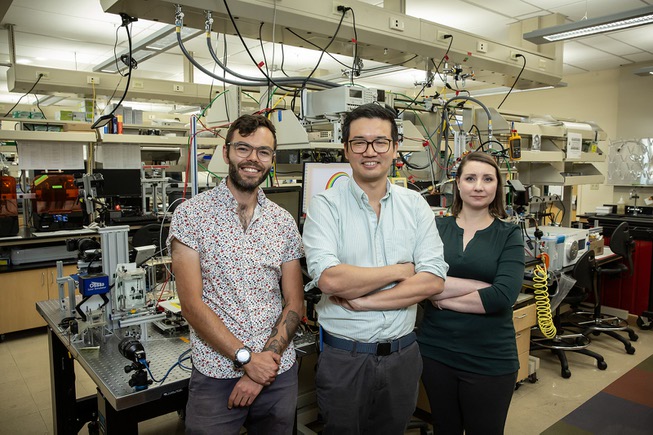
From left, professors Andrew Martin, geochemistry, Jeremy Cho, mechanical engineering, and Marie-Odile Fortier, civil and environmental engineering and constriction, pose for a photo in the science and engineering lab at UNLV Tuesday May 8, 2024.
Thursday, May 9, 2024 | 2 a.m.
Three UNLV professors are working on an iron-production method that doesn’t generate carbon emissions, part of an effort to clean up one of the world’s dirtiest industries.
The U.S. Department of Energy’s Advanced Research Projects Agency-E awarded 13 teams nationwide three-year, $2.1 million grants to develop a new way of processing steel that generates fewer emissions than a traditional blast furnace. The funding comes from the DOE’s national Revolutionizing Ore to Steel to Impact Emissions, or ROSIE, program, which launched last year.
The iron and steel industry accounts for 7% of global greenhouse gas and 11% of global carbon dioxide (CO2) emissions, according to the Energy Department.
“Iron and steel manufacturing is widely recognized as among the most difficult industrial sectors to decarbonize, owing both to the sheer tonnage of product and the dependence on carbon at every step of the process,” the ROSIE webpage states.
Jeremy Cho, mechanical engineering professor and lead researcher for the UNLV team, said he knew he could find a chemistry-based solution, but didn’t know nearly as much about carbon emissions or iron’s geology.
“It’s a big, difficult problem,” Cho said. “And that’s something I didn’t have a lot of specific knowledge on.”
The team also includes Andrew Martin, a UNLV geoscience professor, and Marie-Odile Fortier, an environmental engineer. They began working last summer.
Cho pitched processing the iron ore in an aqueous environment at a lower temperature, like the way copper is produced. Their prototype will consist of an enclosed box full of an electrolyte solution, probably sodium hydroxide or potassium hydroxide, fitted with spinning elements and electrode sheets.
After pouring finely ground iron ore into the box and closing it, an electric current will heat the box to temperatures under 100 degrees Celsius.
Spinning elements will kick into gear, spurring the chemical reaction that will extract the pure iron deposits from the ore. The iron will gather on the electrodes, while leftover impurities can be discarded.
Dev Chidambaram, a chemical and materials engineering researcher at UNR, will help the team choose what materials to use. Ben Xu, a mechanical engineering professor at the University of Houston, will also assist with the design.
“We’re aiming to generate 10 kilograms (about 22 pounds) of iron over 10 hours,” Cho said.
The blast furnace process produces carbon dioxide and hazardous particulate that spews from what Cho describes as “a large chimney.”
“Usually with industrial processes, heat is very difficult to decarbonize,” Fortier said. “Typically, you’re dealing with a fossil fuel you’re burning.”
By contrast, the team’s proposed solution can be powered by renewable energy, making it even more decarbonized.
“It’s more electricity than the conventional process uses, but it’s completely electric,” Fortier said.
Martin, a geoscientist, says the more noniron material is mixed in with iron ore, the more heat it takes to process and separate out the iron.
“There’s a diversity of iron ore deposits, it’s not one size fits all,” he said.
The project focuses on low-grade taconite deposits that consist of roughly 50% iron and 50% silica and other gangue, or worthless, minerals.
Fortier said the program’s aims were ultimately commercial, and the team has been discussing trying the technology on a bigger scale with processing companies.
“If you’ve got a blast furnace, that’s not something anyone wants in their backyard,” Fortier said. “But if you have a much safer process, there might be some potential sites where this could be set up.”
Martin said most of the nation’s iron deposits are located near the Great Lakes. The biggest producers of the 2.6 billion tons of iron shipped globally each year are Australia and Brazil. Most gets shipped to China to be processed into steel, which then gets shipped worldwide.
“If you could potentially (process steel) next to the mine site … I’m sure it’s a crazy reduction in CO2,” Martin said.
[email protected] / 702-948-7836 / @musettasun