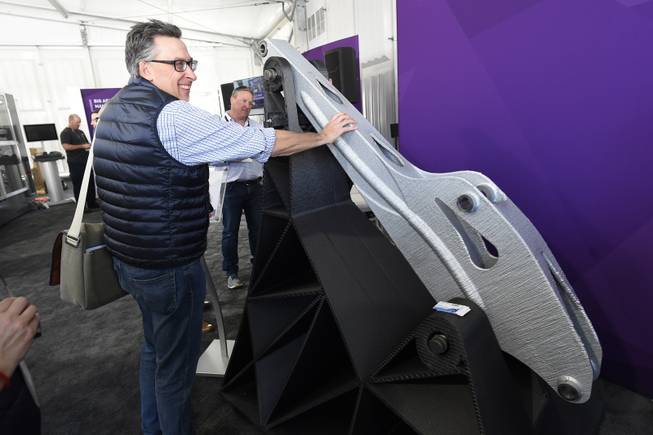
Sam Morris/Las Vegas News Bureau
Dave Bullard examines a 3-D printed “stick,” part of an excavator, during the first day of the 2017 CONEXPO-CON/AGG convention Tuesday, March 7, 2017, at the Las Vegas Convention Center.
Saturday, March 11, 2017 | 2 a.m.
The massive construction vehicles garner immediate attention at CONEXPO-CON/AGG 2017 concluding today at the Las Vegas Convention Center, but it's what’s tucked behind those monstrosities that could have the biggest impact.
With advances in autonomous vehicles, drones and 3-D-printer-created machinery, the construction industry is taking notice, as evident by the tagline of this year’s show, “Imagine What’s Next.”
The Tech Experience displayed the technology in a 75,000-square-foot area filled with sleek futuristic structures, housing various companies and their technologies.
Autonomous attenuators
Attenuator trucks, also known as crash trucks, serve as a protection barrier between traffic and work trucks in roadside construction areas.
The trucks are fitted with a scorpion attenuator, which is a fold-up cushion that takes the shock of the impact, designed to protect the driver in the truck and the work crews ahead.
“If someone isn’t paying attention to the road, falls asleep at the wheel or is drunk and they go into the work zone, they are going to slam into the back of our attenuator truck. That has a big cushion on the back and absorbs the crash,” said Samantha Schwartz, autonomous TMA truck marketing manager at Royal Truck & Equipment.
There are about 2,500 attenuator trucks on the road in the U.S., but operators are increasingly difficult to find because of the danger that is involved, Schwartz said.
Despite the safety cushion, attenuator truck drivers are still in harm's way and many crashes result in injury, Schwartz said.
“The driver of the crash truck gets up every day and says, ‘OK, honey, I’m going to go drive the crash truck today,’ and he’s just praying he doesn’t get hit by a semi truck,” she said.
Royal Truck & Equipment has started work on a driverless attenuator truck, in partnership with Micro Systems Inc.
“We launched this technology in August 2015, and it’s taken about a year to advance this technology,” Schwartz said. ”We’re getting ready to work with our first department of transportation (DOT) to launch our first test program on a highway at the end of this month.”
Schwartz said the truck will launch on a billion dollar project in London. She said the goal is to have U.S. regulations in place by the end of this year to permit completely autonomous attenuator systems.
Once that occurs Royal Truck can start rolling out its autonomous attenuator program with a short list of transportation departments in the U.S. waiting to get in on the new technology, including Nevada, Schwartz said.
Schwartz was hesitant to talk about pricing of an autonomous attenuator truck, but she said it wouldn’t cost much more than a current attenuator truck, which varies in cost by state.
Royal Truck had a virtual reality simulator, created by Virtual 3D Solutions, to show what it feels like to be in the attenuator truck in a work zone, including when it gets hit.
3-D-printed excavator
When people hear about 3-D printed technology, what usually comes to mind are smaller objects that one can produce from their home.
Bucking that trend at the CONAGG-CONEXPO show is the AME (Additive Manufactured Excavator) Project.
The boom (or stick) and the cab of the excavator were 3-D printed, while the other components were manufactured.
“The stick was done with steel, and the cab was made with an ABS carbon fiber composite,” said Clayton Greer, a graduate student at Georgia Tech who worked on the stick of the excavator.
The two features took different amounts of time to print, as the steel-made stick took longer than the carbon-fiber composite cab.
“The stick took about five days, 24 hours operation, with 13 miles of weld wire,” Greer said. “The cab took about seven hours or so for the whole thing.”
The stick was created with a welding torch on a robot arm in a process that is similar to multipass welding, which had more than 900 passes, Greer said.
Pricing the 3-D-printed excavator is tough, according to Greer, as the project was a one off.
Attendees were taken back by the excavator because they weren’t aware such technology existed.
“There is technology here that I didn’t even think was out or even commercially ready. It’s awesome,” said Luke Meyer, an exhibitor working closely with Project AME.
The ultimate goal of the AME project was to show what can be done with 3-D printer technology.
“For one it's a demonstration that we can make structural components with additive manufacturing,” he said. “Also, at this scale — to show that we can make something this big.”
Drone Zone
With drones being more routinely used in a variety of applications, it was a matter of time before the construction industry jumped in the mix.
The netted Drone Zone at the convention features an obstacle course to give attendees an opportunity to see how drones operated. Attendees were invited to wear a first-person viewer headpiece, similar to a virtual reality headpiece.
Adam Negron, president of Las Vegas-based Drone Reviewer LLC, said he set up the Drone Zone for entertainment and education purposes, to give those who attended a chance to fly a drone.
“We’re pushing first-person view (FPV). The idea is to show that you can use drones in first-person view to get a better angle of a site. People who are good at it can go through small spaces to address an issue through the live video,” Negron said.
All hopeful drone operators must first give a simulator a try first. Once they display they can keep the correct altitude and maneuver through various zones correctly, they get to operate an actual drone in the Drone Zone.
Negron said lot of the attendees said they want to or already use drones for surveying for real-time results.
“For example, a man said he has a concrete company, and he wanted to be able to get a better view of a site faster. He can send a drone up and look,” he said. “So this shows what drones can do, and not just in the first-person view, but just in general.”
Negron said most people weren’t very coordinated in the simulator, but a certain segment of participants were noticeably better at it.
“Gamers are naturally good at it because of their hand-eye coordination,” he said. “Some people just shoot them straight in the air, because they keep on throttling up and they’re not just spatially aware.”
Join the Discussion:
Check this out for a full explanation of our conversion to the LiveFyre commenting system and instructions on how to sign up for an account.
Full comments policy